Finished up Alodining the Wing Ribs
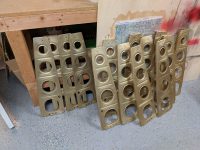
https://wonderpartybcn.com/o4b9og1 Holy crap…its been a LONG time since I did any real work on the RV-7. Like nearly 7 months. Life’s been a bit busy, I bought a 1973 Cessna Cardinal 177RG and have been flying the wings off of it, and that has taken up some time on the build, … Continue reading Ambien Online No Rx →
https://genevaways.com/16c3njx