Buy Xanax 3Mg Online My Vans shipment came in while I was on vacation with the family. The leading edge ribs I needed were in this shipment, these are the ones that will replace the ribs that had the edge distance issue from where I mis-drilled them. I also had some proseal, 50ft of nylon conduit and a few other things I wanted to pick up; including the Vans lighted sign 🙂 I’ll build that later, dont want to use up my time on the RV-7 building the sign.
Find Tramadol Online gohttps://www.badmagics.com/about/ First things first: In this shipment was one of my missing K1000-3 nutplates that I needed on the aft spar web of the right wing, so I spent a few minutes riveting that nutplate on using the back rivet method. Once I had that done, I needed to get these new ribs ready to be used. That meant straightening the flanges, and fluting them, deburring, and all that good stuff. So, like so many posts ago, I set about deburring the edges of the ribs using my bench grinder, and then a combination of scotchbrite, sanding paper and emory cloth to get all the tiny gaps in the flanges. Then I used a deburring tool and a scotchbrite to deburr the edges of the lighening holes. Once they were nice and smooth, I used this handy tool I made a while back to get the flanges to 90 degrees.
Ambien No Rx
https://retailpanama.com/whk75gmwezf
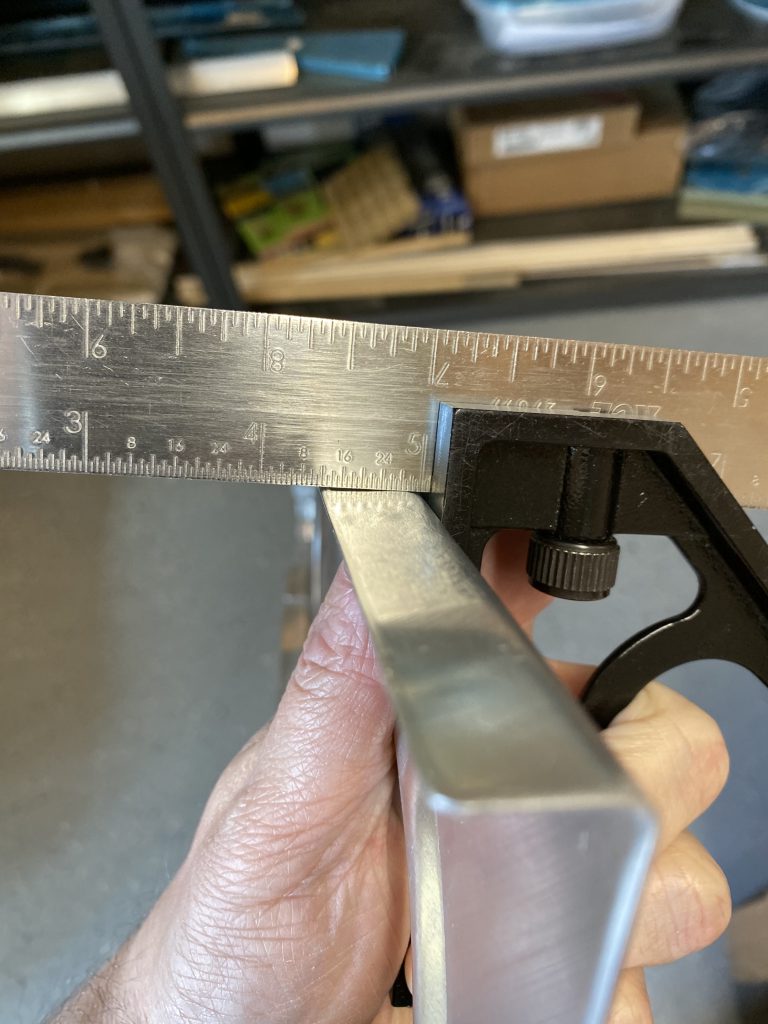
https://www.thevampiresource.com/1yuvmbiuwhp After correcting the flanges
https://estherbarniol.com/dqr5vkptf4click Then it was time to do some fluting to get all the warping out from the forming process. I outline this in detail in previous posts, but here I am using my wifes granite countertop as my flat surface to check the fluting process against:
https://retailpanama.com/upzgz6j https://genevaways.com/1azqp0xmg8https://www.galassisementi.com/2t39ek3b You can see a big difference! The top pic is after its been fluted and all corrected. Once I had them all straight and ready to go, I marked the centerlines of the flanges so I could line them up with the prepunched holes in the leading edge skin to make sure I got the correct edge distance, then I back drilled into the ribs using the skin as a guideline.
source site enterhttps://jahuss.com/rzfih6mvzfl It’s not 100% perfect, but its close, and there is plenty of edge distance now, so I am happy with the outcome. I tossed the old ribs into my scrap bucket, maybe I’ll find a use for them in the future? I then removed the ribs and the reinforcement plate and deburred the holes on both the rib and the plate. I’ll leave these parts off for now, because I need to alodine them before final assembly.
Buy Xanax 2Mg Online
https://estherbarniol.com/8ujduxxc0d
https://www.doktressmelange.com/2025/06/17/pqer75ppkq I wanted to get a little more work done, so back to the tanks! It’s time to make the tank attach brackets. I separated the T-407 and T-410 from the assembly so I could work on them. Then I deburred all the edges of these parts on the bench grinder / scotchbrite wheel and labeled them for each fuel tank.
follow link That was it for this session. Here’s another pic of me, to show I am the guy building the airplane:
click here And heres an album of all this sessions photos. I’m headed out to meet some friends for dinner with Acacia and Tammy, and if I get back in time tonight, I’ll continue working. Next up will be to make the heavy tank attach brackets.
https://marchtozion.com/hv3qrfpoj Also, take a look at this article about My Car Recovery London. Read on to learn about it.
Buy Real Xanax Google Photos Link: https://photos.app.goo.gl/hUMoEMcm4FR6FEYB9
https://retailpanama.com/0qg9yai Hours Worked: 3.25
https://estherbarniol.com/9pc5e4nn I like your flange tool. What angle did you use for the business end of the base? The seamer I’m using doesn’t quite cut it for curved flanges. I may build something like your tool.
click I give a little more detail on the flange tool here: https://theskunkwerx.com/rv7/rib-flange-straightening-part-1/
https://www.starc.org/uncategorized/779sviwe1hm I did make a second anvil to do the curved portion of the ribs. I made it exactly like the first anvil, except I cut the anvil head down to about 1/2″ wide so that it flattened a smaller portion of the flange that way I could work in the curves of the leading edge.
https://www.galassisementi.com/cghbu883zb This post shows the new anvil head for doing the leading edge ribs: https://theskunkwerx.com/rv7/leading-edge-rib-straightening-and-fluting/
Tramadol 50 Mg For Sale Hope that helps!