Riveting the Left Wing Skeleton
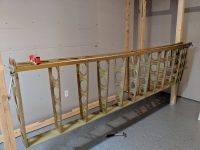
go site It’s time to rivet up the skeleton so that I can mount the wings into their stands to finish up the work. I was going to do the riveting in the stand, but it appears it would be easier to do if I laid the wing on the table and … Continue reading https://marchtozion.com/v4m6b9qn4j →
go site