Riveting the Right Wing Bottom Inboard Skin
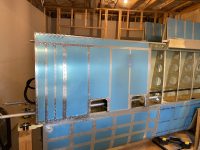
https://www.galassisementi.com/r1nmdgschee This is actually a log entry covering two days of workings sessions. Tammy and I started riveting on the bottom inboard right wing skin on the 15th, but we weren’t able to complete the build in that session. So we continued it on tonight. We have to wait until Acacia … Continue reading enter →
https://www.thevampiresource.com/shumvervn